
Hafnium Price Forecast for 2025 and Beyond: Long-Term Growth Despite Recent Price Corrections
October 9, 2024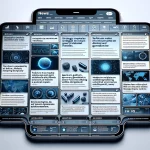
Weekly News Review October 14 – October 20 2024
October 20, 2024Welcome to our weekly news review.
SOUTH KOREA AND THE PHILIPPINES TO COOPERATE ON STRATEGIC METALS:
The two countries agreed to enhance cooperation in various high-tech fields and infrastructure projects.
On Monday, the Philippines and South Korea agreed to upgrade their relations to a strategic partnership aiming to deepen cooperation in various high-tech fields, including energy, critical minerals, artificial intelligence, 5G, and the defense sector. The agreement was signed by South Korean President Yoon Suk-yeol and Philippine President Ferdinand Romualdez Marcos in Manila during Yoon’s two-day state visit to the island nation. In a joint statement, the two sides highlighted their existing partnership, emphasizing that the elevated ties would mutually benefit both countries.
South Korea’s high-tech industry comprises semiconductors, electric vehicles, and robotics. Despite being home to such raw material-hungry sectors, the country needs more domestic sources of critical minerals, making it highly import-dependent. The Philippines, on the other hand, has a substantial mining sector. The island nation is the world’s second-largest producer of nickel, a metal mainly used to manufacture stainless steel and a vital cathode element to produce batteries. In addition, the country mines other goods, such as copper, cobalt, chromium, gold, and silver, according to the US Geological Survey. Under the elevated partnership, South Korea and the Philippines will work together to strengthen the supply chains of critical minerals.
The two countries also agreed to collaborate on significant infrastructure projects in the Philippines. One such project is the Laguna Lakeshore Road Network, which will connect the three central Philippine islands of Panay, Guimaras, and Negros, Yonhap News Agency reports. In addition, the Philippine Department of Energy and Korea Hydro & Nuclear Power signed a Memorandum of Understanding to cooperate on energy, including conducting a technical and economic feasibility study on the potential rehabilitation of the dormant Bataan nuclear power plant.
USA: DEPARTMENT OF ENERGY TO FUND PROJECT TO RECOVER STRATEGIC METALS FROM COAL WASTE:
The Illinois Rare Earth Novel Extract & Supply (IRENES) project aims to strengthen domestic supply chains while addressing the mining legacy.
The US Department of Energy has awarded funding to a project that seeks to recover critical minerals from coal mine waste. The Illinois Rare Earth Novel Extract & Supply (IRENES) project plans to conduct Front-End Engineering and Design (FEED) necessary to establish a fully integrated, vertical supply chain for multiple critical minerals within Illinois.
The Illinois State Geological Survey at the Prairie Research Institute, University of Illinois Urbana-Champaign, leads it. According to the Institute, all solid materials within the waste stream will be converted to products for further use, strengthening domestic supply chains while addressing environmental challenges posed by mines.
In February, the DOE first announced that it would fund IRENES and two other projects seeking to uncover rare earth elements and other critical minerals from coal waste streams. The project has now been fleshed out: Besides rare earth elements, IRENES plans to recover lithium, nickel, zinc, cobalt, manganese, and potentially high-purity aluminum.
The researchers propose two facilities for this: The first is planned near coal mines and waste sites in southern Illinois, focused on extracting and concentrating critical minerals while converting the remaining solid waste into building materials. The second one, located at APL Engineered Materials, Inc. in Urbana, Illinois, will focus on refining mixed rare earth elements into oxides and metals.
Waste From the Last Industrial Revolution Could Fuel the Next One:
Charles Bopp, the project’s co-principal investigator, highlighted the potential impact for Illinois: “The IRENES project will use wastes from the last industrial revolution to supply materials for the next industrial revolution while fostering sustainable economic growth in disadvantaged communities. “
IRENES is not the first project seeking to recover critical minerals from coal mine waste. Efforts to repurpose mines have been ongoing for a while, especially in states with a long coal-mining history. Mining critical minerals could give coal mines a second life and bring back jobs to the states lost in the advent of the coal phase-out.
A team from West Virginia University led by Dr. Paul Ziemkiewicz has made significant progress in extracting rare earth elements from acidic mine drainage and has received multiple funds to expand the project since. Other projects use algae and bacteria to uncover the coveted raw materials.
UNITED KINGDOM: GOVERNMENT AWARDS MILLIONS TO BOOST DOMESTIC MINING OF STRATEGIC METALS:
A new project with representatives from research and industry aims to advance the extraction of critical minerals.
The United Kingdom aims to boost its domestic mining industry and improve the supply of raw materials for green and digital technologies. With roughly $6 million in funding, according to a BBC report, a new Green Economy Centre at the University of Exeter is set to accelerate the extraction of minerals such as lithium, tin, and tungsten in the counties of Devon and Cornwall. The funds are being provided by UK Research and Innovation (UKRI), the national funding agency for science and research.
The joint project involves companies such as Cornwall Resources Limited (CRL), Petrolab, Geolorn, and local government agencies. It aligns with the UK’s critical minerals strategy and supports the responsible sourcing of raw materials, writes CRL’s parent company, Strategic Minerals plc. The center will focus on technical challenges related to emerging mineral deposits and partnerships with local communities.
In April 2023, the British Geological Survey identified many promising areas for extracting critical minerals, some of which had already seen the extraction of raw materials in the past. However, the geologists emphasized that much more research is needed, as only some promising areas will necessarily become a mine.
CANADA INVESTS IN INFRASTRUCTURE FOR STRATEGIC METALS PROJECTS:
A multimillion-dollar investment is set to aid the development of critical minerals in northern Ontario.
Resource-rich Canada aims to establish itself as a leading producer of critical minerals and a future alternative to resource giant China. The government has announced an investment of more than $10 million to advance the necessary infrastructure. The funding will support several projects in northwestern Ontario focused on extracting lithium and copper, operated by companies such as Green TM Resources Canada, Rock Tech Lithium, Frontier Lithium, and Generation PGM. Specifically, the funds will be used for the construction or expansion of road and rail connections, power infrastructure, and the inclusion of Indigenous communities.
According to the government, the national Ministry of Natural Resources must first review the projects. The funds will be provided through the Critical Minerals Infrastructure Fund (CMIF), a key component of Canada’s Critical Minerals Strategy.
“Developments like these help mines get built faster, and they are a key element in seizing the generational opportunity before us,” said Jonathan Wilkinson, Canada’s Minister of Energy and Natural Resources. In July, a multimillion-dollar funding package for expanding infrastructure for critical minerals projects in British Columbia was already announced.
The Canadian government highlights the “enormous economic opportunity” the domestic sector for critical minerals offers in its statement. 2022 the industry contributed nearly 80 billion USD to the gross domestic product. With increasing demand for these raw materials for green and digital technologies, further growth in the sector is expected. Before a new mining project begins, however, many years or even decades often pass; as shown in our infographic, building the infrastructure typically takes about five years.
EUROPE: NEW PARTNERSHIP AIMS TO ACCELERATE SUSTAINABLE BATTERY RECYCLING:
Iondrive uses biodegradable solvents to recover critical minerals without acid-leaching.
Australian-based battery recycling company Iondrive has signed a Memorandum of Understanding with the Dutch Organization for Applied Scientific Research TNO to advance the commercialization of its battery recycling technology. Under the non-binding agreement, the two sides seek to validate Iondrive’s proprietary recycling technology and establish additional industry partnerships.
Iondrive uses biodegradable organic solvents to recover critical minerals from lithium-ion batteries. According to the company, this avoids acid leaching, reducing the recycling method’s overarching footprint. Batteries are mainly recycled by shredding and pre-treating end-of-life batteries into a uniform powdery mixture known as black mass. The mixed cathode and anode material substance contains critical minerals such as lithium, cobalt, nickel, manganese, and graphite.
It is typically shipped to Asia for processing as Western countries lack the necessary processing capacities. Iondrive aims to refine black mass into battery-grade levels and further valorize them into precursor cathode material for battery production, known as PCM. According to the company, there currently needs to be commercial-scale pCAM manufacturing in Europe, creating a gap in the value chain. Through the commercialization of its technology, the company plans to bring it to the Western market to fill this gap. Iondrive added that a pre-feasibility study will be completed later this month.
Mining giant Glencore also recently expanded into battery recycling, announcing the construction of Europe’s largest battery recycling plant in Sardinia.
The agreement with TNO follows the signing in August of a collaboration agreement between Iondrive and the Chair of Production Engineering of EMobility Components at the German university RWTH Aachen to advance sustainable battery recycling methods (PDF).
While focusing on battery recycling, Iondrive also has a subsidiary in South Korea that holds multiple lithium, rare earth elements, and precious metals exploration projects.
USA: INDIANA COMPANY COMMENCES PRODUCTION OF RARE EARTH PURIFIED OXIDES –
ReElement, a subsidiary of American Resources, produces light and heavy rare earths in Noblesville, Indiana. It is the only facility in the world to produce lithium and rare earths.
U.S.-based critical minerals company ReElement Technologies has announced that it has begun daily production of light and heavy rare earth oxides at its plant in Noblesville, Indiana. According to ReElement, the subsidiary of American Resources Corporation can process different kinds of feedstock, including recycled material and fresh ores, and produce oxides for customer deliveries.
Operations focus on producing rare earths for magnet production at a 99.5% purity: the light rare earths neodymium and praseodymium, as well as the heavy rare earths dysprosium and terbium. It complements existing lithium carbonate production at the same facility.
Mark Jensen, CEO of ReElement, highlighted that the facility only produces lithium and magnet-grade rare earth oxides; other companies would focus on either and have designated plants. Jensen added that the company works with multiple ores and recycled material providers to supply its second facility in nearby Marion. Additional equipment for increased magnet recycling and ore processing is being ordered.
In April, ReElement announced it expanded the exclusive use of patents developed at Purdue University for ligand-assisted displacement (“LAD”) chromatography. According to the company, the process is more environmentally friendly than conventional solvent extraction and offers more flexibility in processing different feedstocks. The company added that it can increase production. However, it did not provide an estimated production quantity.
Currently, China dominates the global rare earth processing and refining. Other countries, including the United States, are trying to diversify their supply chains and ramp up domestic capacities to reduce dependencies on the People’s Republic. Partnerships with allied countries are also part of this. A critical minerals agreement with resource-rich Australia is set to be finalized later this year, Australian Premier Anthony Albanese said last month.
GERMANY: CALLS FOR STRENGTHENING THE CIRCULAR ECONOMY –
Reducing bureaucracy and embedding recycling in product design: VDM and BDSV publish a position paper on battery recycling.
To strengthen the supply of raw materials for electric mobility, the Association of German Metal Traders and Recyclers (VDM) and the Federal Association of German Steel Recycling and Disposal Companies (BDSV) are calling for better political conditions for sustainable battery recycling. With the increasing production of electric vehicles and the growing number of end-of-life batteries, the associations’ position paper suggests that the automotive industry should be held more accountable.
They argue that recyclability must be embedded in product design to avoid challenges in disassembly and prevent quality losses in the recovered materials. Furthermore, regulations need to be harmonized, and bureaucratic hurdles reduced both nationwide and at the EU level. For example, according to the associations, the classification of batteries from abroad differs between federal states, being treated as hazardous waste or green-listed waste.
The paper also highlights the need for more processing capacities for “Black Mass,” a critical intermediate product of battery recycling that contains valuable metals like nickel, cobalt, and lithium. The associations are also advocating for support with investments and faster approvals, welcoming the German government’s recently approved raw materials fund.
Batteries and many of the raw materials required are predominantly produced in Asia, especially China. To reduce this import dependency, the EU’s Critical Raw Materials Act, which came into force this year, promotes more recycling alongside domestic mining. Various projects have already been initiated, such as Vulcan Energy’s lithium extraction in Germany’s Upper Rhine Valley.
Additionally, mining giant Glencore plans to build Europe’s largest battery recycling plant in Sardinia, while another newly announced project aims to close a gap in the value chain. Some projects are receiving EU funding, including the construction of a battery factory in Germany by the Swedish company Northvolt.
USA: NIRON LAUNCHES WORLDS FIRST RARE EARTH FREE MAGNET FACTORY –
Commercial-scale production from 2026. Materials are more accessible to source, the company claims.
US magnet startup Niron Magnetics has commenced operations at its pilot magnet plant in Minneapolis, Minnesota. According to the company, the facility is the world’s first rare earth-free permanent magnet factory. Instead of rare earth elements, Niron only uses iron and nitrogen, which are more easily accessible, Niron added. The strongest commercially available permanent magnets, neodymium-iron-boron or NdFeB magnets, are made of an alloy containing roughly 69 percent iron, thirty percent rare earths, and one percent boron.
However, industry participants are skeptical regarding the potential widespread adoption of iron nitride magnet compounds. John Ormerod, head of magnetics and metal consultancy JOC, told industry service Fastmarkets earlier this year that iron nitride has a lower resistance to demagnetization, making it an “unlikely candidate” for electric vehicle traction motors, one of the main fields of application of rare earth magnets besides wind turbines and electronics.
China Dominates the Industry:
Niron stated that the commercial pilot facility has a production capacity of roughly five tons of magnets per year. In its full-scale manufacturing plant, which was recently announced to be in nearby Sartell, Minnesota, Niron plans to produce 1,500 tons of permanent magnets annually from 2026—a low amount, considering that market leader China exported 52,660 t of rare earth permanent magnets in 2023, customs data show. The People’s Republic accounts for roughly 90 percent of global rare earth magnet production.
Companies worldwide are ramping up efforts to increase production to address this import dependency. For example, E-VAC Magnetics, the US subsidiary of German magnet maker VAC, is constructing a magnet-making plant in South Carolina. MP Materials, operator of the only US rare earth mine, Mountain Pass, is building a manufacturing plant in Fort Worth, Texas.